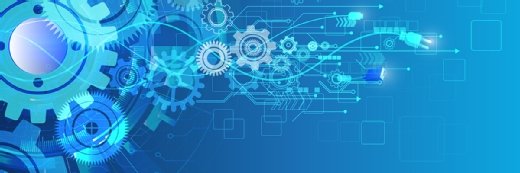
Getty Images/iStockphoto
ERP and APS: What are the differences?
Manufacturing companies may find their ERP software isn't fulfilling their needs. Learn how APS can help with challenges like capacity planning and what-if scenarios.
While ERP software may fulfill some manufacturing companies' business management needs, others may require more help with scenarios like capacity planning and labor shortages. An Advanced Planning and Scheduling application can help solve those problems.
Companies can use ERP software to digitize and automate processes across their business. However, an ERP may not be able to handle more specific manufacturing challenges, requiring companies to seek out an Advanced Planning and Scheduling (APS) application.
Here's a deeper look at ERP software and APS as well as some situations in which companies may need to purchase APS in addition to their ERP.
What is ERP?
Often first implemented to help a company's finance and accounting departments, ERP can also support teams in HR, manufacturing and warehousing, among others. As companies grow, they frequently have trouble maintaining their organizational data and using it to make decisions.
The benefits of using an ERP include the fact that it is a single database, offers a consistent look and feel across its modules and features, and provides reporting and dashboards. ERP software can help a manufacturing company improve its production planning processes, but an ERP's functionality may not be able to handle the needs of complex and fast-changing manufacturing environments.
What is APS?
As the name implies, an APS application concentrates on manufacturing planning and scheduling. As a manufacturing company grows, IT leaders may determine the organization needs to implement an APS application, as manufacturing facilities require detailed plans and schedules to ensure materials and resources will be available to meet customer delivery commitments. An APS application also allows users to adjust schedules as required for situations like delays in receiving materials or the need to expedite an order.
The APS should be able to integrate with the ERP so a company can use the ERP's data for the APS as well and continue to use the ERP software for financial needs as well as other functions that the APS does not offer.
ERP and APS
Here are a few examples of situations in which a company may want to consider purchasing an APS application in addition to their ERP:
Challenges with purchasing materials
If a company's supply chain is unreliable, the manufacturing team may have to regularly adjust production to ensure they are using the facility at maximum capacity. Doing so is easiest with an application that allows users to adjust the plan and schedule without having to rekey all the data, like an APS.
An APS includes reports and dashboards that can show users the results of changing the schedule -- for example, causing delays on one product line because another is postponed -- and highlight potential issues, such as overlapping schedules or employee resource constraints.
Labor shortage
If a manufacturing facility is short-staffed, leaders may have to assess the effect of slowing production on certain product lines and decide which products to focus on. APS can help them make those decisions.
APS can also potentially help leaders make decisions about employee costs by showing them the consequences of, for example, using overtime to fill the gap or reducing production in the short term.
What-if scenario analysis
An APS application provides more comprehensive tools and algorithms for what-if scenarios than ERP software. These capabilities can help users create production plans and adjust the plans as needed.
For example, a customer may request a delivery date be moved up. Before making a commitment to the customer, employees must understand the effect that doing so will have on other customers and delivery dates, and they can calculate it using an APS application. An APS can also prove helpful if a user is trying to calculate the number of products to manufacture to ensure machines and manufacturing workers are employed most effectively.
An APS allows users to make these types of calculations and switch from one scenario to another without reentering data multiple times.
Capacity planning
An APS also provides functionality for capacity planning. Company leaders must be able to calculate the amount of product that the organization can manufacture in a certain amount of time so they know how much they can sell. Overestimating the number of products that the organization can create in a given time can lead to missed deadlines and upset customers, while underestimating leaves machines idle and workers under-utilized.
An APS can also help a company plan for the future. If company leaders want to expand their manufacturing facilities, they need access to historical data so they can estimate the amount of additional space, equipment and resources they'll require.