MIT researchers demonstrate a new technique for rapid 3D printing using scrap metal and beds of sand-like glass beads
3D-printed results may look crude, but are strong enough to withstand milling and machine finishing.
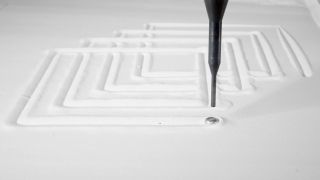
Researchers at MIT have developed and published a new technique called liquid metal printing "LMP" that, while limited in terms of resolution, is both fast and is said to avoid the warping and cracking seen in more traditional metal printing methods. A demonstration of this application was presented by making frames for chairs and tables in a few minutes.
The researchers used the LMP method to ensure it can print a reliable enough structure needed for different applications. Naturally, there will be fine-tuning before such 3D printers can be mass-produced and used in many industries. However, this 3D printer shows that it is reliable enough for its intended use.
This 3D printer has a furnace that melts the aluminum, which can be scrap pieces, and stores the molten metal in a crucible, ready to be used. The machine then outlines the shape needed by the user beneath a sand-like surface made of 100-micron glass beads which absorb the heat, solidifying the metal.
Throughout the process, the temperature controller maintains 700 degrees Celsius consistency until it is poured through its nozzle tip. Once printed, the melted aluminum quickly cools down to take shape, ready to be removed and processed further. Once the printed aluminum is milled and drilled as needed, it becomes ready to be assembled and used. The MIT researchers show the entire process in the video below, where the frame of a table and chair are printed.
This research was funded by automotive components maker Aisin Group, Amada Global, and a US-based furniture company Emeco. It's not surprising to see companies from these respective fields fund such projects, which could greatly benefit their industries.
Since aluminum can be recycled multiple times, one can also use this method to make prototypes. The LMP process also allows one to print with variable thickness, providing enough durability needed for msilling and boring processe once a product is printed.
Why Aluminum?
The research paper explains that the primary purpose of this method is for the building sector, though one could apply this to many fields if it's developed and deployed accordingly. The aerospace and automotive industries are other obvious examples, particularly when it comes to making prototypes. LMP wastes little or no aluminum material as scrap during its manufacturing process, which should add to its appeal, especially when you combine this with the strength of the end product compared to alternative methods that use things like powdered metal.
Since 3D printing now involves different materials like food and resin in place of filaments, it would be nice to think metal 3D printing might also make it to the home enthusiast market at some point. But since this method involves a furnace holding molten aluminum, it's more likely that after some optimization and streamlining, it might find use in smaller-sized businesses, eventually.
Stay On the Cutting Edge: Get the Tom's Hardware Newsletter
Get Tom's Hardware's best news and in-depth reviews, straight to your inbox.
Roshan Ashraf Shaikh has been in the Indian PC hardware community since the early 2000s and has been building PCs, contributing to many Indian tech forums, & blogs. He operated Hardware BBQ for 11 years and wrote news for eTeknix & TweakTown before joining Tom's Hardware team. Besides tech, he is interested in fighting games, movies, anime, and mechanical watches.
-
atomicWAR
ROFL...I came to comment when they can 3D print wheelchairs (paraplegic here), then talk to me about it. I would love to skip all the vendors and just make my own. After 26 years using a chair, I know exactly what I like. And yes comfort is key so I won't be a first gen adopter.derekullo said:Solving the problem of needing the cheapest most uncomfortable chair possible! -
pug_s I doubt that this idea is original. If you watch youtube videos, you can watch people pour molten aluminum on ant nests and then dig up the remains of it.Reply -
Notton
That ant nest method you are thinking of is called "sand casting", and it's ancient.pug_s said:I doubt that this idea is original. If you watch youtube videos, you can watch people pour molten aluminum on ant nests and then dig up the remains of it.
However, unlike sand casting, there is no need to painstakingly prep the mold to get the shape you want.
Looking at the video, the "resolution", or level of detail, looks awful, but it can print complex shapes. -
Findecanor It indeed looks like an alternative to sand casting.Reply
I wonder which alloys that are viable. There are alloys more suitable for casting, but parts machined from those have different properties than if machined from an alloy intended for machining.
And why do these researchers don't wear protective masks around those microscopic glass beads?