galvanizing
Our editors will review what you’ve submitted and determine whether to revise the article.
- Related Topics:
- iron processing
- galvanneal process
- coating
- surface treating
- electrogalvanizing
galvanizing, protection of iron or steel against exposure to the atmosphere and consequent rusting by application of a zinc coating. Properly applied, galvanizing may protect from atmospheric corrosion for 15 to 30 years or more. As discontinuities or porosity develop in the coating, galvanic or electrolytic action ensues; the iron or steel, however, is protected by sacrificial corrosion, a phenomenon in which, as long as the zinc and the iron are in contact, atmospheric oxidation spares the iron and affects the zinc.
Zinc may be applied by two general methods: hot dipping and electrolytic deposition.
In hot-dip processes, cleaned iron or steel, usually in sheet form, is passed through a flux such as a zinc–ammonium chloride and guided through a bath of molten zinc. In wire galvanizing, the wire is drawn through successive pickling, annealing, and washing operations. It is dried before passing into the galvanizing pan and is drawn out through wipers of charcoal, coke, sand, or asbestos.
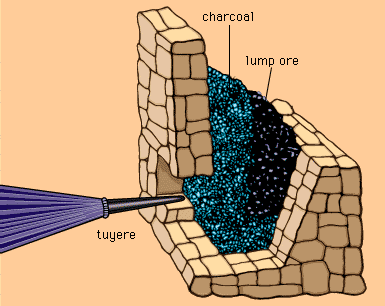
In one hot-dip process, intermetallic compounds of iron and zinc are formed on the surface of the steel or iron being treated by heating it in the presence of finely divided zinc below the melting point of the zinc. In another, molten zinc is applied in a fine spray to the surface of the cleaned iron or steel; the zinc adheres tightly to the surface.
In electrolytic deposition, or electroplating, a pure coating of completely controlled thickness of zinc may be applied without heat. More care is required, and for articles that must be made watertight, the electrolytic processes do not have the soldering effect of the hot processes. The zinc coating, however, has greater adherence than that formed in the hot-dip process. See also sherardizing.